Sunlight Recycling
Sunlight Recycling
Europe's state-of-the-art lead acid battery recycling facility.
More about our processRecycling Plant
Established in 2014 in Komotini, Northeastern Greece, it is one of Europe's most advanced recycling plants.
Operating Activity
The plant supplies Sunlight Group’s Industrial Complex with more than 50% of its production needs in raw lead material.
Sustainability
Continuous effort to balance the growth of our environmental stewardship, business & social progress achieves benefits for all stakeholders.
Green Mission
We are part of "The Green Mission" initiative. It was born from the desire to improve the method of recycling scrap accumulators.
Part of Sunlight Group
Sunlight Group is constantly upgrading our facilities with investments in equipment, automated systems, and human resources to expand Sunlight Recycling’s production capacity.
Our Vision
Is to establish ourselves as a global leading force in the field of lead-acid battery recycling. We are committed to actively contributing to sustainable development and creating value not only for our organization but also for the entire business ecosystem of Sunlight Group. By implementing innovative practices and leveraging our expertise, we aim to revolutionize the way lead-acid batteries are recycled, ensuring optimal resource utilization and minimizing environmental impact.
Our Values
Passion for the Customer
Efficiency & Effectiveness
Accountability
Integrity
Entrepreneurship
Latest news
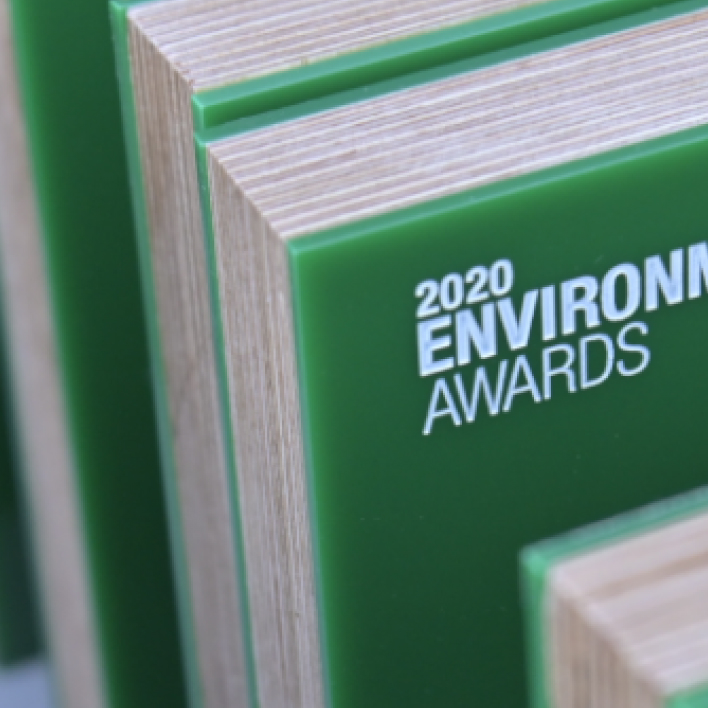
Double distinction at Environmental Awards 2020
We won the gold prize in the “Circular Economy” category and silver in the “Emissions Control Technology” category.
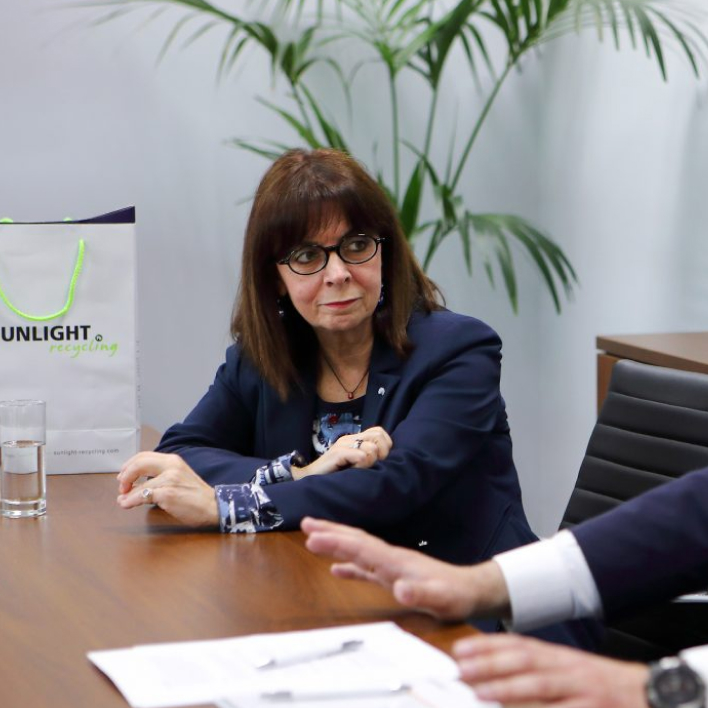
President of the Hellenic Republic visits Sunlight Recycling
Katerina Sakellaropoulou in our Battery Recycling Plant in the Industrial Area of Komotini.
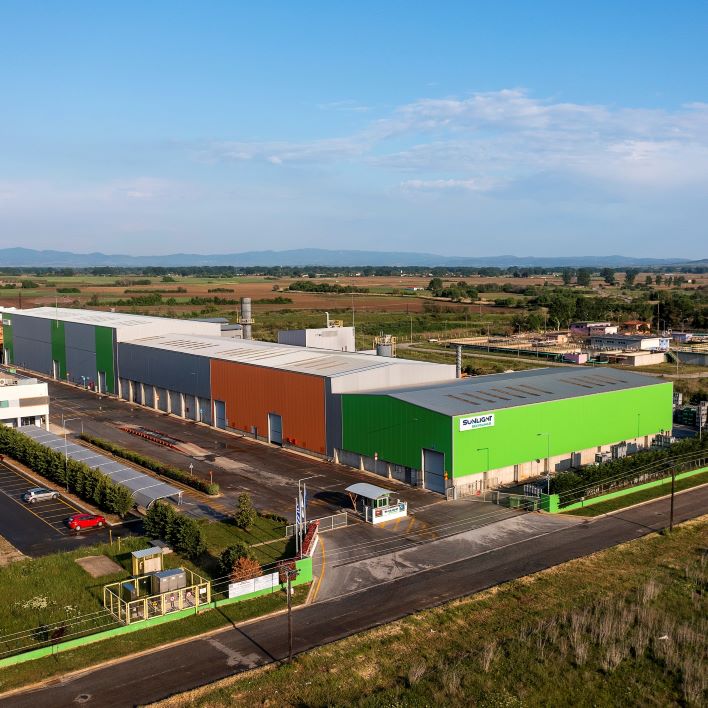
Recycling more than doubles production capacity
The expansion will bring the facility to the top of single unit recycling plants.